Screw Boss Design Guideline
Our Recommendation
The following design recommendation is frequently found in literature and on the internet:
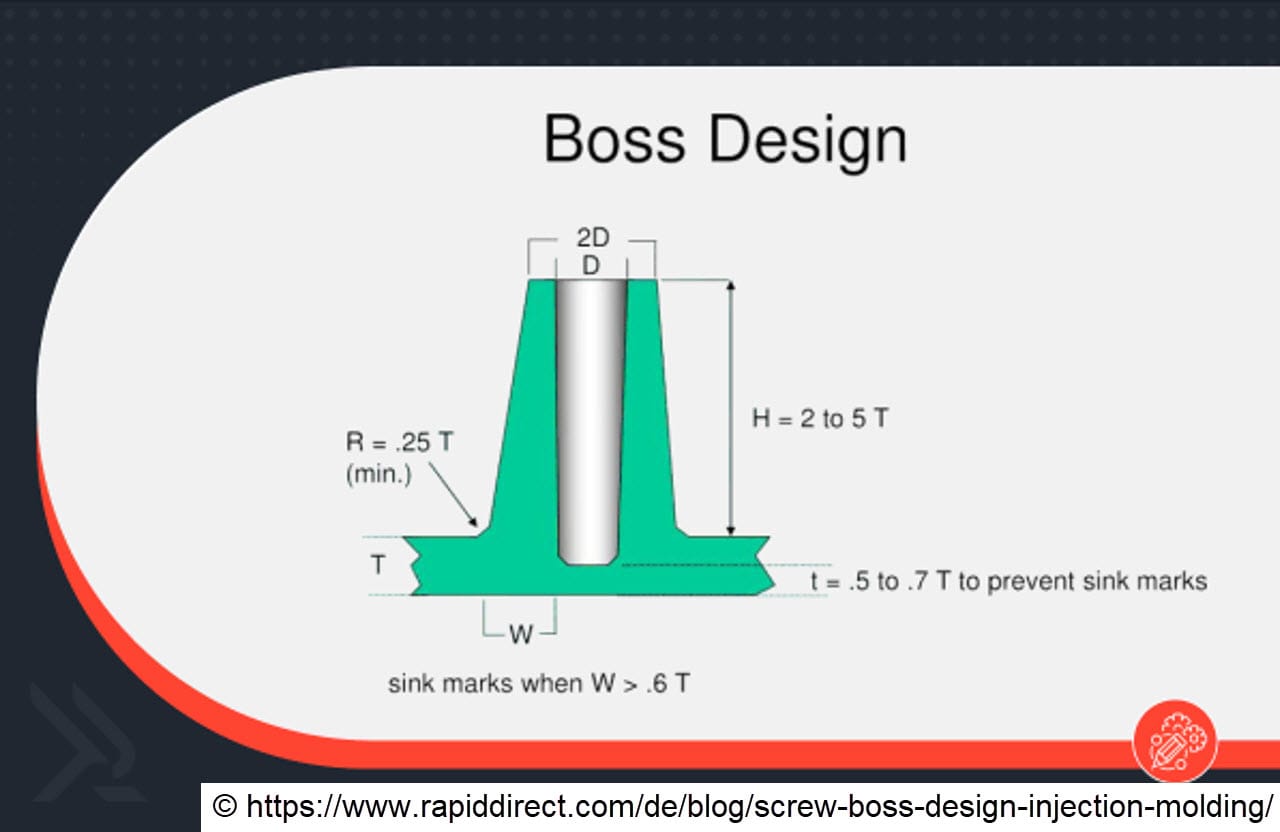
However, this can become problematic, especially for screw bosses that need to be slightly taller, since the condition W > 0.6T can no longer be met due to the draft angle and the resulting wider base of the screw boss.
For this reason, we have developed and successfully implemented the following design guideline for our screw bosses:
We taper the wall thickness in the area of the screw boss to allow for the most uniform wall thickness possible with smooth transitions. This ensures that the “largest possible enclosed circles” remain nearly the same size. In the example above, we used the following values:
a = 1.0 mm
b = 3.0 mm
cabove = 1.0 mm
dbelow = 2.3 mm
Width of the recess: 2.3 mm
With these values and a surface texture (e.g. VDI 3400-27) on the opposite side of the screw boss, we have had very good results, with no visible sink marks. The recess should be generously filleted to ensure smooth transitions.
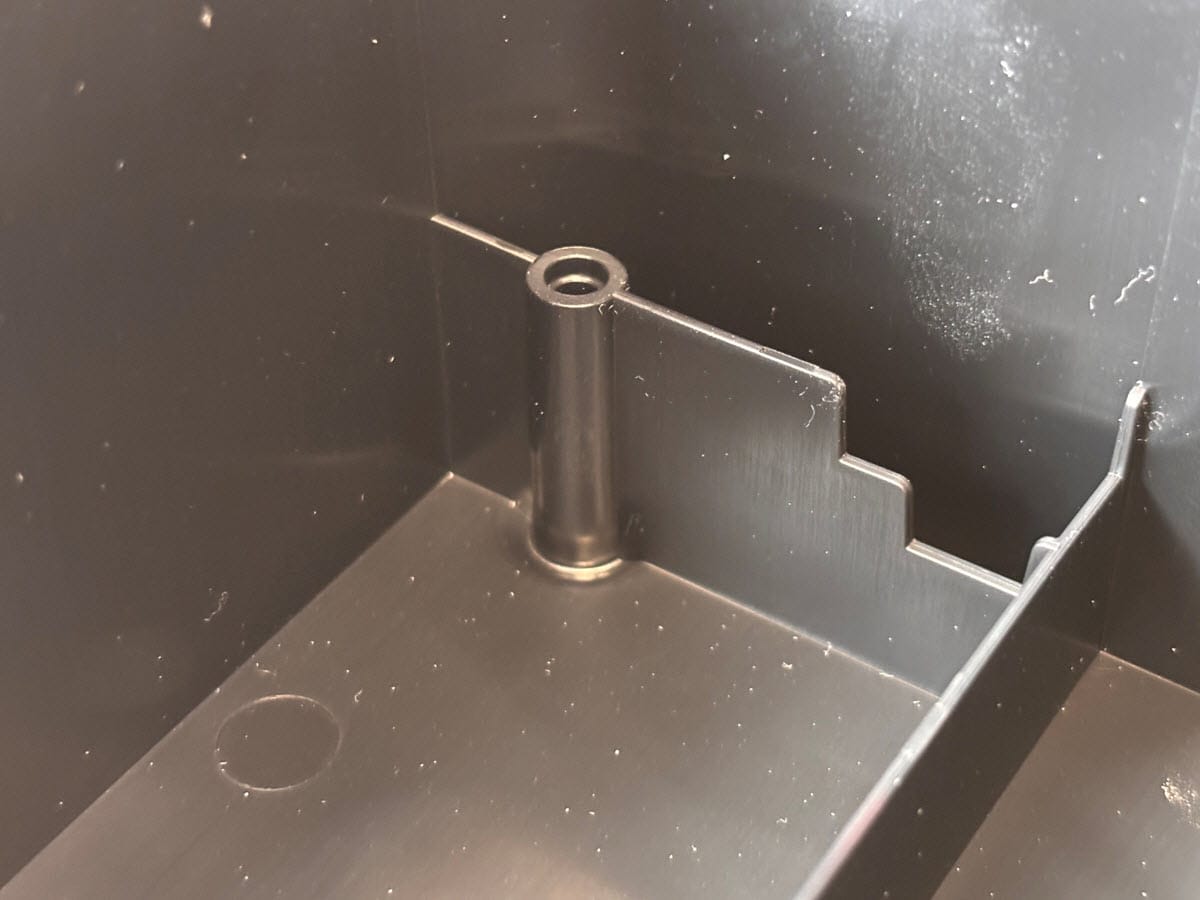
Basic Design Guidelines for Screw Bosses in Plastic Components
The following general design guidelines should be considered during the design process.
1. Wall thickness of the boss
Recommendation: The wall thickness of the screw boss should be approximately 50–60% of the nominal wall thickness of the surrounding part.
Advantage: Reduces the risk of sink marks and internal stresses in the material.
Disadvantage: Walls that are too thin may compromise mechanical strength.
2. Höhe des Doms
Recommendation: The height should be 2 to 3 times the outer diameter.
Advantage: Ensures sufficient thread engagement depth for screws.
Disadvantage: Overly tall bosses can lead to cooling issues during injection molding.
3. Fillet radius at the base of the boss
Recommendation: A radius of 0.25 to 0.5 × the nominal wall thickness.
Advantage: Reduces stress and improves material flow.
Disadvantage: An excessively large radius can lead to material buildup.
4. Draft
Recommendation: At least 0.5° on the outer surface and 0.25° on the inner surface of the boss.
Advantage: Facilitates demolding and reduces tool wear.
Disadvantage: Insufficient draft can cause ejector issues.
5. Positioning of the boss
Recommendation: Bosses should not be placed directly on outer walls.
Advantage: Prevents sink marks on visible surfaces.
Disadvantage: May require additional ribs for reinforcement.
6. Connection with ribs
Recommendation: Use ribs with 50–67% of the nominal wall thickness.
Advantage: Increases stability and distributes loads evenly.
Disadvantage: Ribs that are too thick can lead to sink marks.
7. Spacing between multiple bosses
Recommendation: At least twice the nominal wall thickness.
Advantage: Prevents cooling issues and material buildup.
Disadvantage: Insufficient spacing can affect the part quality.
Further links on the topic: